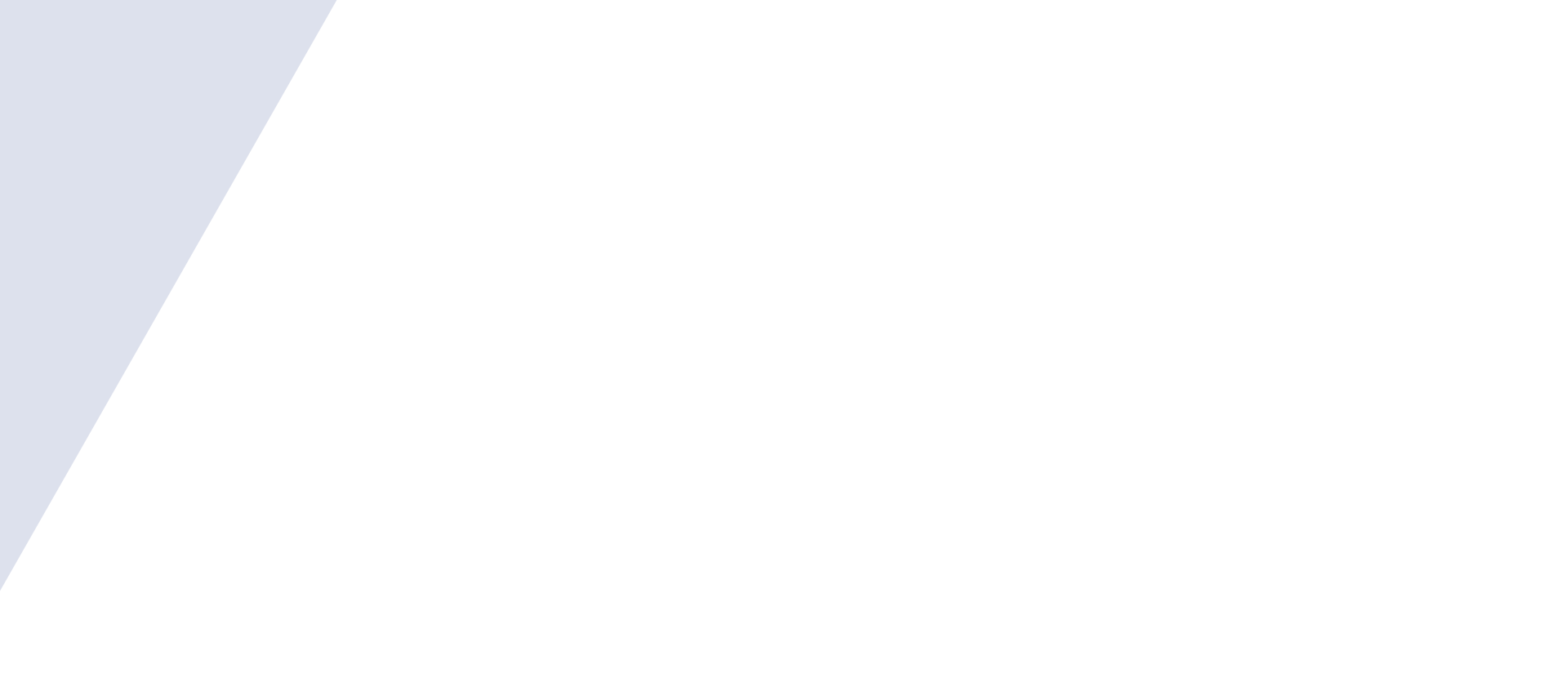
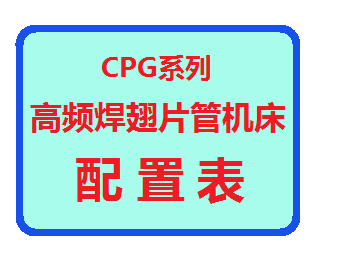
The configuration table
Company Profile
Heilongjiang Province A City Huaguang Energy Saving Equipment Co., Ltd. was established in 1999, is the production of high-frequency welding finned tube machine tool professional manufacturers, CPG series products have been formed, the annual production capacity of 60 setsThe machine tool from the gear box to the development of dual-frequency program control, the machine to fully automatic working condition, with automatic clamping, automatic on, feeding function, welding part of the use of three-dimensional electric adjustment, support part of the use of electric adjustment.. The stability of the machine is good, simple operation, advanced technology, reliable quality. One of my company's CPG-9 type, CPG-9 type I, CPG-10 type of the company's patented product. CPG-9 type I, CPG-10 machine has been sold all over the country, and out of the country, exported to Canada, Germany, Mexico, Russia, Ukraine, Iran, India, Kazakhstan and other countries, praised by foreign customers. At the same time, the company has two finned tube production line, the production of finned tube 3,000 tons, finned tube series radiator 20,000 sets, to many businesses have brought huge benefits.
Let us with the consistent unity, hard work and dedication, with the full use of existing resources to the fastest speed to expand the market, create greater success, to ensure that Huaguang company in the high-frequency welding finisher machine manufacturing industry vanguard status The Let us join hands, put into new opportunities and challenges, proactive, good governance, with Huaguang unique wisdom and spirit to create Huaguang's new heyday.
CPG series of high-frequency welding finned tube machine technical parameters table:
1, CPG-8 type (length of 8 meters) support the use of gear box form
Technical parameters: pitch 4.5mm-16mm 8 kinds
Steel pipe: diameter φ20mm-φ114mm
Strip: thickness 0.8-2mm Width 10mm-25mm (not greater than the pipe radius is appropriate)
Bed standard length of 8 meters, can also be produced according to customer requirements.
Supporting high-frequency power supply 100KVA, 200KVA
2, CPG-9 type (length of 10 meters) support the use of dual-frequency program control
Technical parameters: pitch 4mm-30mm adjustable
Steel pipe: diameter φ20mm-φ114mm
Steel strip: thickness 0.8-3mm width 10mm-30mm (not more than the steel pipe radius is appropriate)
Bed standard length of 10 meters, can also be produced according to customer requirements.
Machine to achieve semi-automatic working condition
Supporting high-frequency power supply 100KVA, 200KVA, 300KVA
3, CPG-9 type I (length of 10 meters) support using dual-frequency program control
Technical parameters: pitch 4mm-30mm adjustable
Steel pipe diameter φ20mm-φ159mm
Steel strip: thickness 0.8-3mm width 10mm-30mm (not more than the steel pipe radius is appropriate)
Bed standard length of 10 meters, can also be produced according to customer requirements.
Machine to fully automatic working condition, with automatic clamping, automatic on, into the material function
Supporting high-frequency power supply 100KVA, 200KVA, 300KVA, 400KVA
4,CPG-10 type (length 12 m) support using dual-conversion program control
Technical parameters: pitch 4mm-50mm adjustable
Steel pipe diameter φ25mm-φ219mm
Strip: Thickness 0.8-3.5mm Width 10mm-40mm (not more than the pipe radius is appropriate)
Bed standard length of 12 meters, can also be produced according to customer requirements.
Machine to achieve automatic working condition, with automatic clamping, automatic on, into the material function,
Welding part of the use of three-dimensional electric adjustment, support part of the use of electric adjustment.
Supporting high-frequency power supply 200KVA, 300KVA, 400KVA
5,100KVA high-frequency power supply for winding finned tube range ф60 the following, for welding carbon steel, alloy steel.
200KVA high-frequency power supply for winding finned tube range ф114 the following, for welding carbon steel, alloy steel.
300KVA high-frequency power supply for winding finned tube range ф159 the following, for welding carbon steel, alloy steel, stainless steel.
400KVA high-frequency power supply for winding finned tube range ф219 the following, for welding carbon steel, alloy steel, stainless steel.
6,Which CPG-9 type, CPG-9 type I, CPG-10 type, the company's patented product.
7, the machine needs to lengthen the standard size of each additional 1 meter plus 5,000 yuan
Technical description of dedicated machine tool for CPG series high frequency welding finned tube
1 technical description
High-frequency welding spiral finned tube is made of high-frequency welding spiral fins made of a highly efficient heat transfer components. The machine is the production of this high-frequency welding finned tube of special equipment. This product uses Japan's Panasonic PRC automatic control system, dual frequency linkage, simple operation, the use of stable, high degree of automation.
The working principle is to pass the pipe through the automatic pipe system (steel tube holder) to the bedside box of the pneumatic chuck, automatic clamping, bedside box driven by the variable frequency motor, according to the pre-selected pitch and speed drive Steel pipe for the spiral forward movement, steel belt supply institutions will be 0.8-3.0mm thickness of the strip was also spiral wound in the steel pipe. At the same time, the upper and lower contacts of the high frequency welding machine come into contact with the contact line between the steel pipe and the fin, and the skin effect is achieved between the steel pipe and the fins under the action of high frequency current. As the steel pipe for continuous spiral movement, so the strip was a spiral welded on the tube, a high-strength high-frequency spiral spiral finned tube. The finished finned tube is fed to the finished product rack by the automatic unloading system. The machine adopts dual frequency conversion technology, PRC program control, in order to achieve operational automation.
2 Introduction to equipment
2.1 Machine parts:
The special machine tool is mainly composed of nine parts: bed, bed, high-frequency welding head, steel belt supply mechanism, automatic tube system, automatic pinch system, automatic unloading system, water cooling system, electrical control box and PRC automatic Program control system.
2.1.1 bed: the base is welded by high-quality channel, the laying of special rails and sports rack, the inside of the bed with a finned tube body. As well as pneumatic components and machine tool control components.
2.1.2 Bedside section:
2.1.2.1 using 5.5kw variable frequency motor cycloid reducer; driven by the high and low speed sprocket wheel rotation. According to the need to achieve a variety of speed.
2.1.2.2 3.0kw variable frequency motor by the gearbox and worm gear reducer driven gear and rack bite to achieve the longitudinal movement of the bed part. The variable frequency motor is controlled by the PRC program to achieve the pitch adjustment (pitch 4-50).
2.1.2.3 3.0kw variable frequency motor by the gear box and reducer; gear and rack bite, to achieve the bed part of the fast return to the car.
2.1.2.4 pneumatic chuck by the QGB200 cylinder through the rod control to achieve automatic loading of steel pipe.
2.1.3 high-frequency welding head:
This system is one of the key parts of the machine, its function: 1) clamping steel pipe and with the bed chuck to keep coaxial. 2) with guide pulley and pressure roller mechanism, can be precisely wrapped around the steel pipe, guide and pressure in place, easy to weld and winding. 3) With the upper contact and the lower contact movement mechanism, it is convenient and accurate to push the upper and lower contacts to the steel strip and the steel pipe, to maximize the high temperature, reduce the resistance, to meet the welding conditions, in order not to make high frequency Current loss, the system are made of stainless steel and copper and other special materials. 4) to achieve high-frequency welding power and mechanical parts of the docking. 5) Surface water cooling system required for carrying the welding.
2.1.4 steel belt supply institutions:
This mechanism consists of the material tray, the belt conveyor, the pulley and other parts, the steel strip placed on the tray rotation, so that the steel strip in a continuous and orderly manner, the conveyor belt automatically sent to the belt, Through the force of the cylinder, can make the steel belt into the high-frequency welding head before the stretch, conducive to the correct winding steel.
2.1.5 Automatic pipe system: 1) the steel frame on the rack through the pneumatic device to the stall. 2) from the upper and lower cylinder and cycloid reducer motor drive pipe system to the pipe to the chuck card. 3) The pallet holder is supported by the steel pipe before winding and winding process, and is required to be coaxial with the bed chuck to ensure the smooth movement of the steel pipe.
2.1.6 Automatic feeding system:
By the finished material rack and pneumatic control of the mechanical arm. Can automatically send the finished finned tube to the finished product rack.
2.1.7 water cooling system, air pump: (user-owned)
Used to cool high-frequency power supply, high-frequency welding contacts and pressure pulley. It is composed of water tanks, water pumps, pipes, valves and other components. The cooling effect is the key to success and durability in the welding process. Cooling water according to the power supply should be no less than 20 cubic meters. Air pump selection pressure 1.0MPa volume of 0.3 cubic meters above 380V voltage.
2.1.8 The electronic control box and the PRC program control system are the control center of the operation equipment. All the movement (including mechanical movement, pneumatic and high frequency power supply) is controlled and displayed by it to ensure the safe and reliable operation of the equipment.
2.1.9 machine technical parameters:
2.1.9.1 finned tube pitch range: 4-50mm free choice;
2.1.9.2 strip thickness: 0.8-3mm, strip width: should not be greater than the steel pipe radius;
2.1.9.3 Outside diameter of steel pipe: ф20mm-ф159mm;
2.1.9.4 Welding rate: ≥85%;
2.1.9.5 Welding line speed: ≥ 15 m / min.
3 supply list
Equipment Name Device Composition / Model Quantity
High frequency welding finned tube
Special equipment CPG series of high frequency welding finned tube machine 1 set
GGC100-400KW high frequency power supply 1 set
4 equipment requirements
4.1 Use of the environment requirements:
4.1.1 Indoor installation, high-frequency equipment and finned pipe machine is well grounded, the ground wire color must be significantly different from the control line, the cross-sectional area> 4mm ², grounding resistance is not greater than 4Ω.
4.1.2 Altitude not exceeding 1000 m, otherwise the rating should be reduced.
4.1.3 ambient temperature does not exceed +40 ℃, not less than -10 ℃.
4.1.4 Air relative humidity is not more than 85%.
4.1.5 no severe vibration, no conductive dust, no corrosive gases and explosive gases.
4.1.6 Installation inclination is not greater than 5 degrees.
4.1.7 installed in a well-ventilated area.
4.2 Power grid requirements:
4.2.1 grid voltage should be sine wave, harmonic distortion is not greater than 5%.
4.2.2 The unbalance between three-phase voltage should be less than ± 5%
4.2.3 grid input voltage for the line voltage AC 380V, the grid voltage fluctuation range of not more than ± 10%, the grid frequency change does not exceed ± 2% (that should be between 49 ~ 51Hz).
4.2.4 Power supply: The power supply should be greater than the power required for high frequency power.
5 Scope of supply:
5.1 Scope of supply by supplier
5.1.1 The contents of the third part of the supply list.
5.1.2 to provide equipment to install all the technical information, and to help guide the installation of equipment.
5.1.3 Provision of technical training and operational training.
5.1.4 to provide comprehensive after-sales service and permanent technical advice.
5.1.5 offers equipment spare parts and spare parts.
5.2 Scope of supply
5.2.1 Power supply transformer, field connection cable.
5.2.2 Equipment cooling water site installation pipeline, cooling soft water and primary water system.
5.2.3 According to the supplier plan layout and installation dimensions, the demand side is responsible for the electrical equipment infrastructure.
5.2.4 Installation and commissioning tools and tools for production and maintenance.
5.2.5 The demand side is responsible for the equipment site lifting and equipment installation and installation adjustment.
5.2.6 Tools required for inspection and inspection of finished products.
6 Delivery and Warranty Period
6.1 Delivery time
45 days after the commencement of the contract to complete the design and manufacture of equipment, should be shipped to the demand side of the conditions.
6.2 Warranty period
Warranty period for the equipment commissioning acceptance after 12 months.
7 after-sales service
7.1 After-sales service commitment
7.1.1 Provide technical documentation for installation, maintenance and operation.
7.1.2 Provision of equipment for major consumable components.
7.1.3 Provide technical training for equipment operation and maintenance personnel and undertake permanent technical consultation.
7.1.4 After the equipment acceptance, the supplier to stay a technical staff to monitor the use of equipment, monitoring time is 3 days.
7.15 Responsible for installation of equipment and equipment debugging work.
7.1.6 Responsible for resolving abnormal equipment quality, response time<24 hours (except for force majeure).
7.1.7 After one year of acceptance, the equipment will only charge the maintenance cost and the maintenance cost will be composed of maintenance personnel travel expenses, working hours fee, replacement device cost fee and so on until the equipment is used for one year.
7.1.8 For the equipment purchased by the purchaser, the supplier undertakes that the equipment does not raise the price within two years.
7.2 Technical data delivery and staff training
7.2.1 The following technical documents are provided by the supplier
7.2.1.1 Installation drawings and layout plans (one month of delivery)
7.2.1.2 Equipment input Power cable specification (one month of delivery)
7.2.1.3 Total equipment capacity requirements (one month of delivery)
7.2.1.4 Equipment User's Manual (random delivery)
7.2.1.5 Equipment packing list (random delivery)
7.2.1.6 product quality inspection certificate (random delivery)
7.2.2 Personnel training
7.2.2.1 training demand side operator 2-3.
7.2.2.2 trainers involved in equipment installation and commissioning.
7.2.2.3 During the installation and commissioning of the equipment, technical talks on the principle of equipment, operation, maintenance, external configuration and so on are held by the technical staff of the supplier.
7.2.2.4 During the installation and commissioning of the site, the technical personnel of the supplier shall be responsible for explaining the external connection requirements of the equipment and explain the functions of each part according to the drawings.
7.2.2.5 It is the responsibility of the technician to provide a detailed explanation of all technical advice that does not violate technical disclosure.
7.3 Installation and commissioning
7.3.1 Demand side should be equipped with mechanical and electrical technical personnel, the supplier to help guide the installation of equipment.
7.3.2 Before installation, the supplier shall provide equipment installation size requirements and external connection requirements.
7.3.3 The supplier is responsible for commissioning the equipment and the supplier shall provide all other necessary support in addition to the supplier's equipment.
7.3.4 demand side for the supply of commissioners to provide accommodation convenience.
7.3.5 During the installation and commissioning process, the supplier shall comply with the requirements of the factory management system, subject to the organization requirements, and the technical and technical information disclosed by the demand side to be strictly confidential.
7.3.6 equipment acceptance, the demand side and the supply side of the technical staff to fill out the equipment acceptance.
8 Special Note:
The above technical requirements and price, service commitment for sales in mainland China.
High frequency welding finned tube machine configuration
CPG-8 type (standard bed length 8 meters)
1, the machine adopts rail processing to form the track, the drag part uses 5.5kw electromagnetic adjustment motor output to the chuck through the gearbox, forming 4.5-16mm, 8 kinds of pitch, with fast carriage return function, light pipe bracket, finned tube bracket Automatic control.
2, the welding part of the use of advanced technology to transform the transformer up and down, ultra-thick electrode to minimize current consumption, support part of all the casting after processing.
3, transformers, upper and lower contacts, pipe rack, pressure belt, pressure roller are used pneumatic devices, and a regulator and the table can be adjusted with the pressure.
4, all pneumatic components are used domestic brand pneumatic parts.
5, the original electrical appliances using the original brand name.
6, high-frequency power supply can be configured 100-200KVA power supply
CPG-9 type (standard bed length 10 meters)
1, the machine uses heavy bed, rail with 40Gr forging, milling, grinding processing after forming.
2, the drag part of the use of 5.5kw with tilting reducer inverter motor, the output power to 22kw motor power, pitch with 2.2kw with cycloid reducer frequency motor drive to form a variety of pitch, to achieve automatic return, two-way Jogging function, light pipe support, finned tube bracket are automatic control of the trip switch.
3, around the welding part of the most advanced design process, the main use of casting rough, after machining to ensure its strength and accuracy. Transformer up and down, the distance between the electrode and the conductor to ensure that the current loss of the smallest, the use of copper copper conductive form to ensure reliable contact and lower cost, easy to operate and easy maintenance.
4, transformers, upper and lower contacts, brackets, pressure belt, pressure roller are used pneumatic devices, and at any time on any cylinder pressure regulator.
5, pneumatic original use of domestic brands pneumatic original.
6, the original electrical appliances used in the original brand name.
7, the frequency changer adopts Japan Panasonic frequency changer.
8, automatic program control part of the Japanese Panasonic program PRC controller and Panasonic touch screen the entire working state by the program control.
9, the machine is equipped with power emergency stop device and anti-collision device.
10, high-frequency power supply can be configured according to user requirements 100-300KVA power supply.
11, the entire machine to achieve semi-automatic working condition.
CPG-9 type I (standard bed length 10 meters)
1, the machine uses the national standard channel welding made of heavy bed, rail with 40Gr forging, milling, grinding processing after forming, head and rail to achieve rolling friction.
2, the drag part of the use of 5.5kw with tilting reducer inverter motor output power to 22kw motor power, pitch with 2.2kw with cycloid reducer frequency motor drive to achieve automatic carriage return, two-way jog function, Dual-frequency motor PLC program control, light tube moving frame, finned tube bracket are photoelectric switch automatic control, to achieve automatic length welding.
3, the use of advanced pneumatic card, chuck with advanced domestic pneumatic chuck.
4, equipped with automatic on the body with a feeding frame, feeder, feeding rack and cutting machine, are controlled by the PLC program.
5, around the welding part of the most advanced design process, the main use of casting rough, after machining to ensure its strength and accuracy. Transformer up and down, the distance between the electrode and the conductor to ensure that the current loss of the smallest, the use of copper copper conductive form to ensure reliable contact and lower cost, easy to operate and easy maintenance.
6, transformers, upper and lower contacts, brackets, pressure belt, pressure roller are used pneumatic devices, and at any time on any cylinder pressure regulator.
7, pneumatic original use of Chinese and foreign joint venture brand pneumatic original.
8, the original electrical original brand name is the original electrical appliances.
9, the frequency changer uses the Japan Panasonic frequency changer.
10, automatic program control part of the Japanese Panasonic program PRC controller and Panasonic touch screen to achieve automatic control work.
11, the machine is equipped with power emergency stop device and anti-collision device.
12, high-frequency power supply can be configured according to user requirements 100-400KVA power supply.
13, the entire machine to achieve full automatic working condition.
14, the machine in the design, use reached the domestic advanced level, simple operation, the use of stability.
CPG-10 type (standard bed length 12 meters)
1, the machine is welded in the form of steel structure, the bed with 12mm steel plate and channel welding, the overall stability, the use of 40Gr rails forging, milling, grinding after forming, nose and rail to achieve rolling friction.
2, drag the nose motor with 7.5kw with cycloid reducer, inverter motor, the output power to 30kw motor power, pitch using 3.0kw variable frequency motor by double reducer, to achieve pitch and fast carriage return function, two-way jog Function to achieve dual-frequency motor PRC program control, light pipe support, finned tube bracket and the feeder are controlled by the photoelectric switch to achieve full automatic scale, the middle stop welding, random adjustment of pitch function.
3, the use of advanced pneumatic card, chuck with advanced domestic pneumatic chuck.
4, equipped with automatic on the belt, the feeding frame, feeder, feeder by the PRC program control, finned tube bracket and the use of automatic transfer structure.
5, around the welding part of the use of international advanced design process, the main body of steel, the mechanical processing, the advantages of solid and stable. Transformer left, right, up and down are electric adjustment, light pipe support using electric adjustment, advanced technology, simple and stable operation, can be adjusted. Electrode plate and conductive body from the workpiece to the nearest distance to ensure that the current loss of the smallest power to play the largest electrode twisted copper conductive form to ensure reliable contact, low cost, easy to replace.
6, transformers, upper and lower contacts, brackets, pressure belt, pressure pulley, are used pneumatic devices, are barometer pressure regulator valve, at any time on the name of the cylinder regulator.
7, pneumatic original use of Chinese and foreign joint venture brand pneumatic original.
8, the original electrical original brand name of the original electrical appliances.
9, inverter, touch screen, PRC program controller, photoelectric switch, access switch, reflector and control power are Japan's Panasonic products.
10, the entire machine operation by the PRC program controller to control the program to work.
11, the machine is equipped with power emergency stop and anti-collision device.
12, recommended with high-frequency power supply 200KVA, 300KVA, 400KVA.
13, the entire machine to achieve full automatic working condition.
14, the machine in the design, manufacturing process to achieve international advancedLevel。
COPYRIGHT©2019 Heilongjiang Acheng Huaguang Energy Saving Equipment Co., Ltd.
+8613904667326